Sulphidation and Corrosion Fatigue of High Pressure Turbine Blade (HPTB)
By Strategic Safety Office and Airworthiness Office, Civil Aviation Department
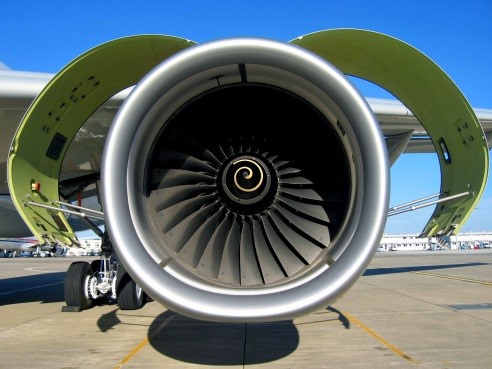
In October 2016, crew of an A330 aircraft with Rolls-Royce Trent 700 engine heard a loud bang during take-off roll at the Hong Kong International Airport (HKIA). Initially it was thought to be a tyre burst but crew got a momentary engine #1 stall message followed by engine #1 failure displayed on ECAM. Crew aborted the take-off. Between December 2016 and February 2018, three other incidents resulted in in-flight shut down were reported to Hong Kong Civil Aviation Department (CAD) by Hong Kong operators of A330 aircraft with Rolls-Royce Trent 700 aircraft engines. Sulphidation of the HPTB in the aircraft engines was noted in each case.
Sulphidation of the HPTB refers to the corrosion of the parent material of the HPTB with sulphur at elevated temperature inside the aircraft engine. Sulphur is normally present in small amount in the jet fuel - a petroleum product similar to kerosene, but may also come from atmospheric contaminants. As the jet fuel is combusted with the engine intake air, a corrosive by-product (eg. sulphate) is stuck to the blade shank and melt at temperature resulting in chemical attack. Over time, cracks might develop and grow on the affected HPTB which eventually fail under high engine power conditions (eg. take-off), resulting in damages to the engine and possibly degrading the control of the aircraft. Investigation conducted by the aircraft engine manufacturer found that as the types of operation and amount of atmospheric contaminants differ among Trent 700 aircraft engines operators worldwide, sulphidation of the HPTB would occur at varying rates. Meanwhile, it was noted that a few more Trent 700 sulphidation events also occurred in other places.
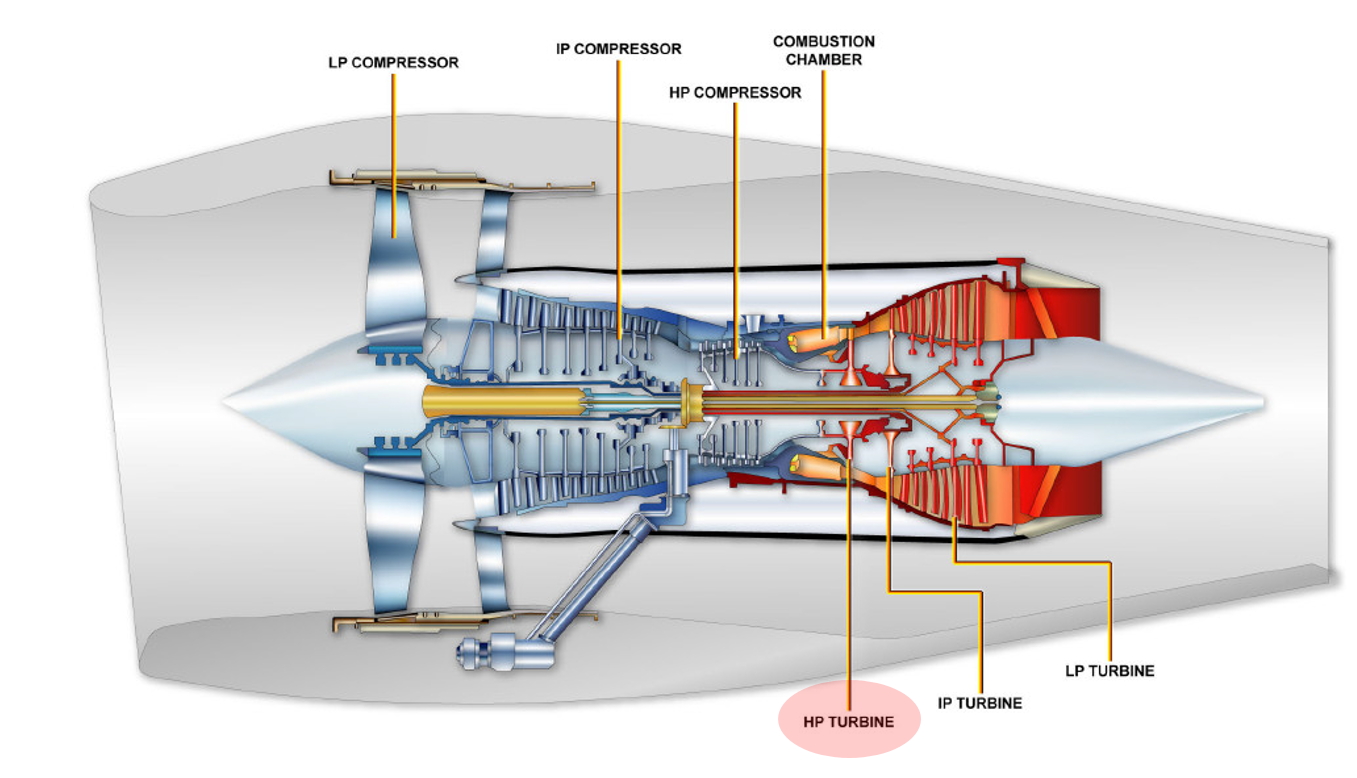
Layout of a typical aircraft engine
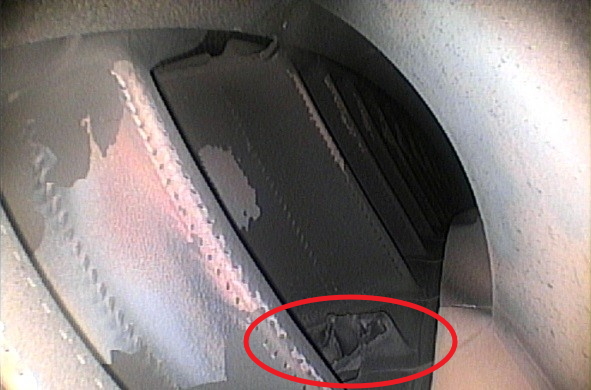
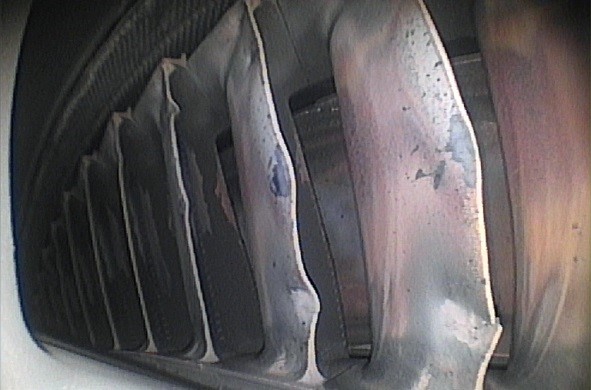
Missing HPTB and damages to the aircraft engine
Since the incident occurred in October 2016, the CAD had been monitoring the situation based on the associated procedures of the CAD in-house risk based approach in accordance with the Mandatory Occurrence Reporting Scheme. This included the reviewing and reporting of cases at different stages within the CAD in compliance with the established procedures. Externally CAD liaised closely with parties concerned, including the operators of the Trent 700 aircraft engines, the aircraft engine manufacturer and the European Union Aviation Safety Agency (EASA), the aircraft engine certification authority, to follow up on the sulphidation issue and to formulate mitigating measures to prevent recurrence of similar incidents. Through the concerted efforts of the various parties, the aircraft engine manufacturer published a Non-Modification Service Bulletin (NMSB) on 26 November 2018. The NMSB instructs operators on when to remove the Rolls-Royce Trent 700 Engines from service, based on specific engine serial numbers, by specified dates, to enable replacement of the affected HPTBs where a higher level of corrosion exposure is expected. The objective is to reduce the risk of aborted take-offs and in-flight shut downs, and to reduce the risk of HPTB release and potential subsequent high energy debris release in aircraft. It is worth noting that the contents of the NMSB have been discussed among CAD, the aircraft engine manufacturer and the aircraft engine certification authority before its issuance. In addition, the Hong Kong operators concerned have also informed CAD that the work required by the NMSB would not impact their operation.
On 21 December 2018, the EASA issued an Airworthiness Directive (AD) to mandate the NMSB. The CAD has since mandated all Hong Kong operators of the Rolls-Royce Trent 700 aircraft engine to comply with the instructions of the EASA AD and the NMSB. The Hong Kong operators concerned have come up with project plans to comply with the AD requirement.
This case illustrated that an effective mandatory occurrence reporting system with a systematic safety data analysis process enabled early identification of possible hazards. Coupled with the establishment of safety information sharing and communication platforms / channels among operators, industry and regulatory partners, proactive safety enhancements can be made to achieve a safer civil aviation system.